Rigid thermal protection systems (TPS) are used on all planetary missions to protect spacecraft from the heat experienced during atmospheric entry. The entry aeroshell drag area is limited by the size of the launch vehicle, which in turn restricts the mass that can be landed on the planet surface. Inflatable decelerators are a promising alternative technology. They could be deployed before entering the atmosphere, allowing missions to land bigger payloads on Mars and other planets.
Heritage rigid TPS cannot be used on an inflatable decelerator; a flexible TPS is needed. Vorticity has led an ESA-funded project to develop a flexible TPS suitable for a Mars-entry inflatable hypersonic decelerator.
This project aimed to build critical technical capabilities for flexible TPS design and manufacture. Our regular UK partners, Fluid Gravity Engineering, provided thermal design, modelling and analysis. The Austrian Foundry Research Institute, ÖGI, performed wide-ranging material characterisation tests while the German Aerospace Centre, DLR, tested the flexible TPS in a Mars-representative arc-jet.
Vorticity’s engineers defined the flexible TPS requirements, then identified and down-selected the best materials for the job. We oversaw a complete mechanical and thermal characterisation test campaign, before establishing and trialling the most suitable manufacturing techniques. The project was completed by manufacturing a sub-scale breadboard, used for packing and deployment tests.
Through this activity, Vorticity established European-leading abilities in entry vehicle flexible TPS design and breadboarding. This knowledge can be transferred to flexible insulation systems on launch vehicles and satellites.
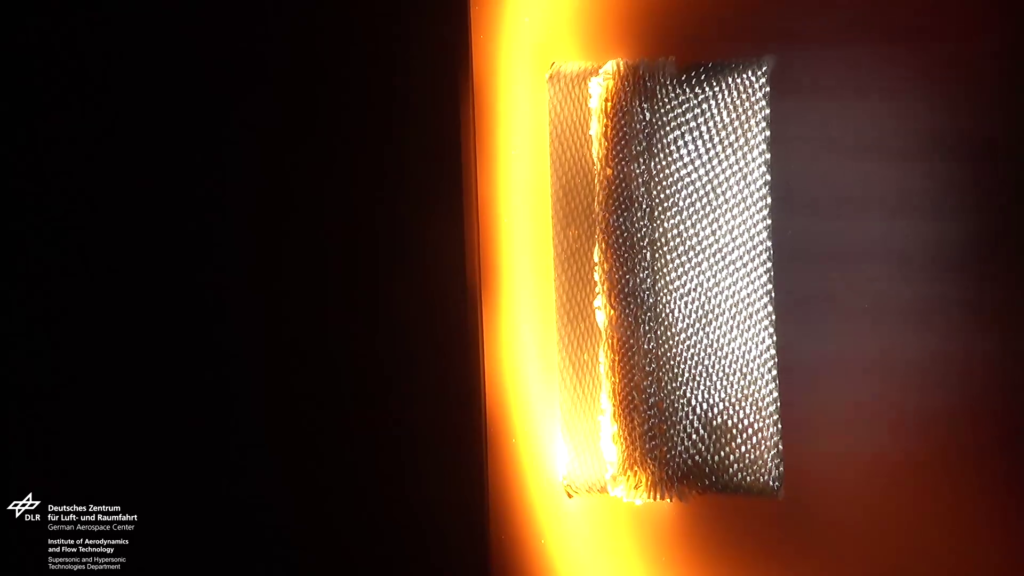