Parachutes used for space missions, and Mars missions in particular, are usually very large (at least 10 m diameter) and manufactured from very lightweight material. If the parachute is reduced in size to allow testing in wind tunnels, it is impossible to scale the material in the same way as the parachute; it would be impossibly thin.
Supersonic tests in large wind tunnel facilities are costly and parachute testing has been limited, by tunnel blockage, to articles with a diameter less than 0.83 m or modest Mach numbers. Full-scale supersonic parachute testing is also expensive; on the order of tens of millions of dollars for a series of tests. Therefore, a test technique that allows supersonic testing of larger subscale parachutes under representative conditions at modest cost is beneficial.
A MAXUS sounding rocket flight provided the opportunity to develop such a test technique.
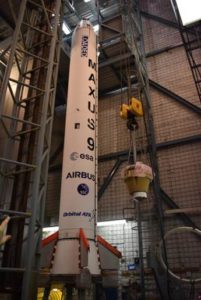
The rocket was able to accommodate a test vehicle attached between the payload and motor section. The test vehicle took the place of a ballast mass, which was previously necessary to optimize the mass properties of the rocket’s payload section. Following burn-out the motor stage separated from the payload section, exposing the parachute test vehicle. After a short delay, the test vehicle was then jettisoned from the payload section.
The velocity at release was 3.0 km/s at an altitude of 162 km. Following the release, the vehicle continued on a ballistic trajectory to 679 km altitude before falling back and re-entering the atmosphere. Once the vehicle had decelerated to Mach 1.7, in conditions which were equivalent to those for a Mars mission, the parachute was deployed, inflated and controlled the descent of the test vehicle to a safe landing. The performance of the parachute was monitored using GPS, accelerometers and high definition video. The vehicle transmitted its position to the ground throughout the descent and the vehicle was recovered shortly after landing.
The 13.7 kg test vehicle and avionics were manufactured by Vorticity in the UK. The heat shield was a 60° sphere-cone as used on the successful Huygens mission. This protected the test parachute from the space environment and the aerothermal heating on re-entry, while providing sufficient stability to ensure the vehicle entered the atmosphere in the correct orientation and sufficient drag to reach the required parachute deployment conditions. During inflation and the subsequent descent to the ground, the vehicle had to acquire position, velocity, orientation and acceleration data in addition to high definition video of the parachute in flight.
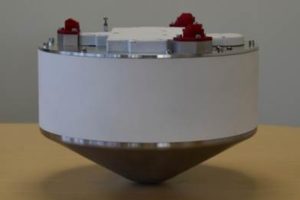
The heat shield was manufactured from solid stainless steel with a tungsten insert to keep the centre of gravity as close to the nose as possible and to soak up the heat of re-entry. At the end of re-entry, the internal temperature of the front shield was only 140°C. The cylindrical section was treated with a ceramic coating to protect it from the lower levels of heat in this region.
The vehicle was controlled by a custom-made data acquisition system which used two GPS receivers to monitor its position and velocity; accelerometers, rate gyros and magnetometers to derive its orientation, and thermocouples to measure its internal temperature. It also included a small radio beacon which transmitted the vehicle position to the ground during flight and a pyrotechnic controller to command deployment of the parachute. Data from all the sensors were recorded in solid state memory and recovered after the flight. Two cameras were flown: one high speed to observe the parachute inflation in detail and a second high definition camera to observe the subsequent flight.
The parachute was deployed at Mach 1.7 by two pyrotechnic devices. The inflation and subsequent flight were captured on high definition video and high-speed data were obtained.
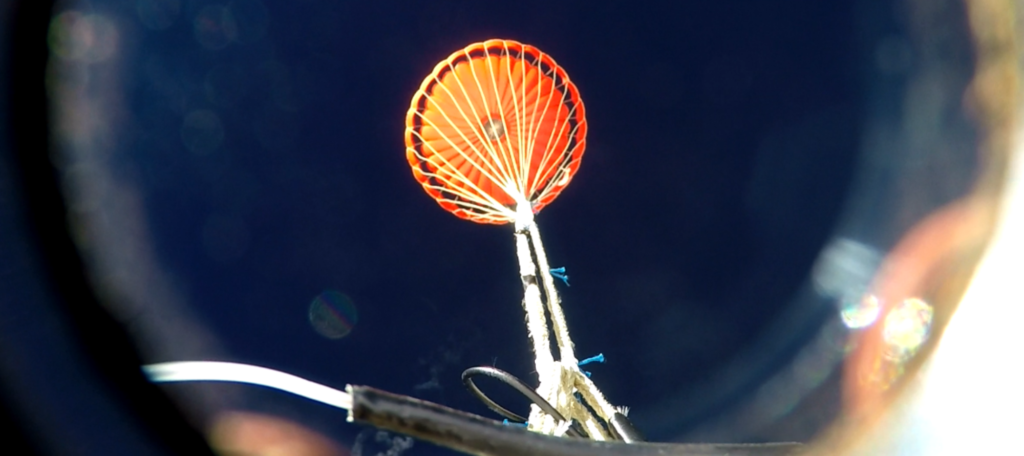
MAXUS9 Liftoff
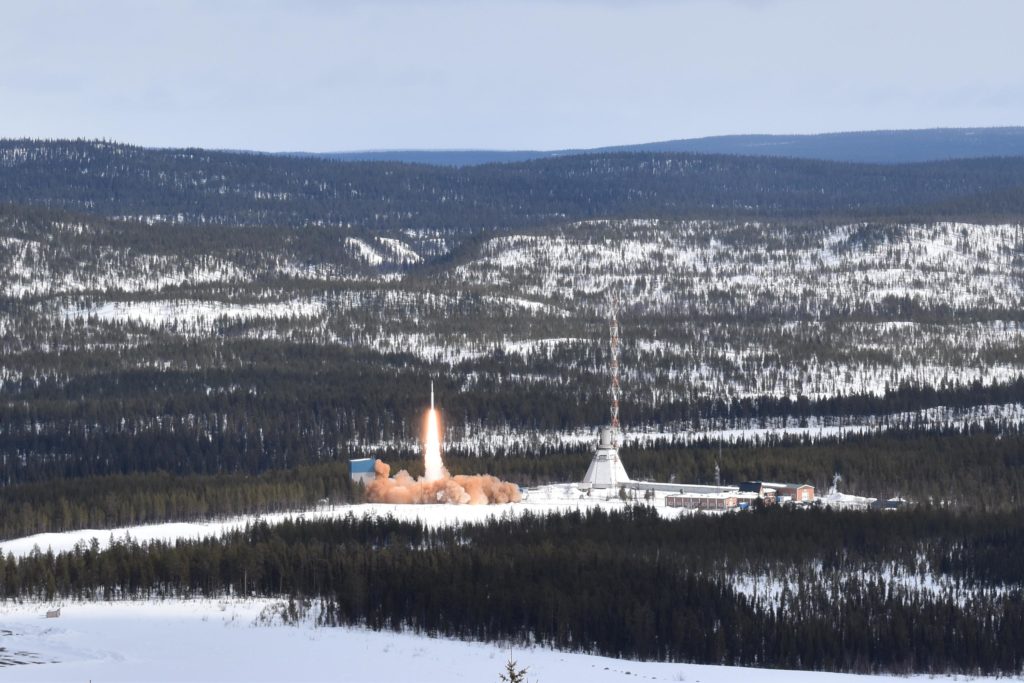
The flight demonstrated Vorticity’s capability to test parachutes in environments equivalent to those experienced on Mars missions. The results have been used to complement existing data from wind tunnel tests, NASA flight tests from the 1960’s and flight data from the recent ExoMars mission. Aerothermal data were also obtained which will aid the development of the next generation of Earth entry vehicles.
The SUPERMAX mission (Supersonic Parachute Experiment Ride on a MAXUS rocket) was flown successfully on the MAXUS 9 flight which took place on 7th April 2017.
Our industry partners
Vorticity collaborated with the Swedish Space Corporation throughout this project and would like to thank the team at Esrange for their support and expert advice. DLR provided the Phoenix-HD GPS receiver and flight software. Fluid Gravity Engineering provided the capsule design support and thermal performance analyses. Walter Kostelezky GmbH & Co. KG designed the parachute bag for the supersonic parachute.
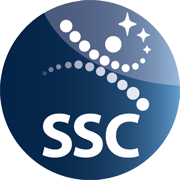
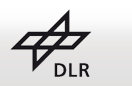
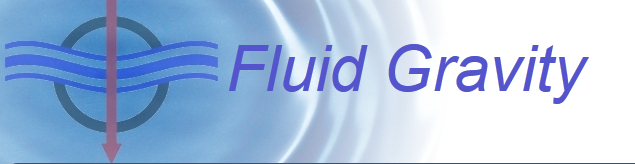