ESA Ministerial to review the way forward for ExoMars
ESA Council has mandated the Director General to terminate cooperation with Roscosmos on the ExoMars rover and surface platform. During ESA’s next Ministerial Council taking place in Paris in November 2022, all ESA Member States will discuss the way forward for the project.
Parachute Assembly Sub-System Engineering and System Drop Tests
Vorticity was responsible for the Parachute Assembly Sub-System Engineering and System Drop Tests. Activities included the performance analysis for developing the high-altitude drop test vehicle and the controller and instrumentation used to conduct an end-to-end test of the parachute system.
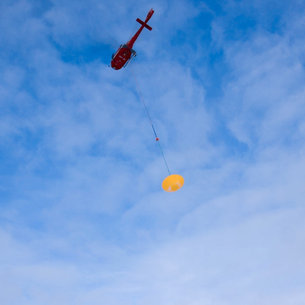
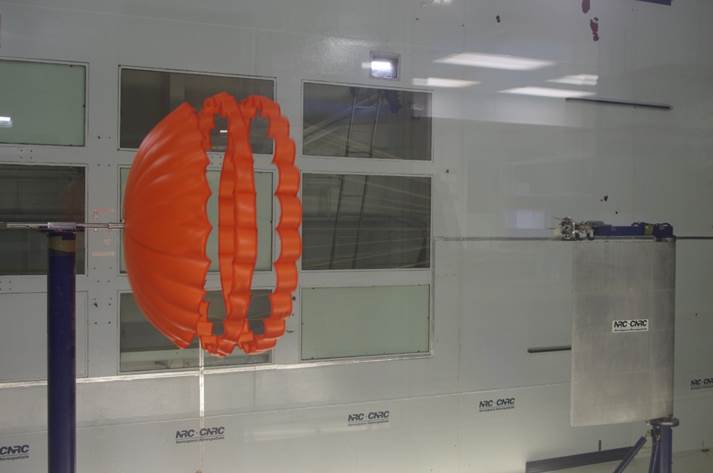
Testing parachutes
Vorticity tested a range of subsonic parachute shapes for the Mars missions as part of the ESA Technology Research Programme. Seven types of model parachute were flown in this test series: two types of
Novel testing methods
In addition to the main test campaigns, two novel techniques for parachute investigation were deployed and developed – Particle Image Velocimetry (PIV) and Pressure Sensitive Paint (PSP).
PIV allows the flow velocity around an object in a wind tunnel to be measured by seeding the flow with fine droplets of fluid, in this case, olive oil was used, and then taking pairs of images a short period apart. These are then analysed to determine the motion of droplets between frames and thus the flow velocity.
A 0.75m DGB parachute was tested in the NRC 2×3m wind tunnel in Ottawa. The results compared favourably with the results of the CFD/FSI analysis of the same configuration.
PSP is used to determine the surface pressure on objects in wind tunnels but has not yet been used for flexible structures such as parachutes because of the flexibility requirements for the paint and the low dynamic pressure at which tests with fabrics must take place.
Progress was made in formulating paints which were capable of being coated onto fabrics and working at the required dynamic pressure. However, an insufficient signal-to-noise ratio was achieved to allow progress to a wind tunnel test of a full parachute.
A total of thirteen tests were reconstructed using the CFD/FSI technique. These included wind tunnel tests in the subsonic and supersonic regimes, parachute inflation, PIV tests and free-flight tests. In each case, the motion of the parachute was replicated accurately and the measured force coefficients compared favourably with those measured in the corresponding tests.
The flow velocity around the parachute matched the observations from the PIV test accurately. This demonstrated the utility of CFD/FSI to help understand the phenomena observed in tests and to extrapolate test results to untestable conditions.
Wind Tunnel Testing
Vorticity managed the subsonic wind tunnel tests of the second stage parachute at the National Research Council of Canada’s 9 m x 9 m wind tunnel.
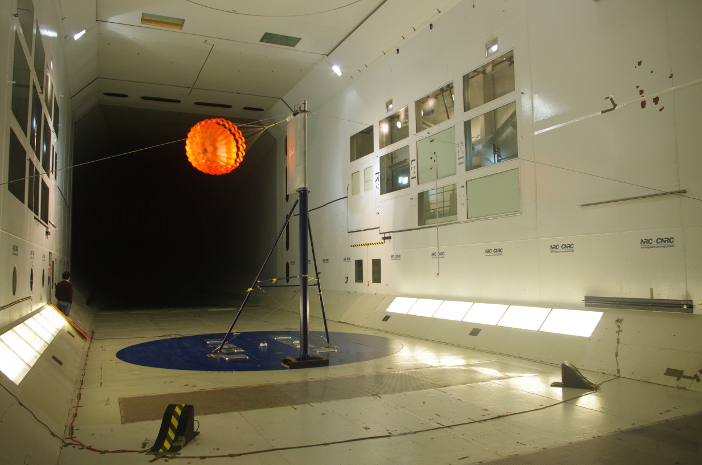
Two types of tests were performed in the wind tunnels in Ottawa: inflation tests where the test parachute was deployed using a drogue and allowed to fly unconstrained while the drag coefficient was determined; and coefficient measurement tests where the parachute was constrained at both the line confluence and vent, while being forced to fly at angles of attack between angles up to ±45° depending on the parachute type.
Vorticity also led the successful supersonic testing of the first stage parachute in the NASA Glenn 10 ft x 10 ft tunnel.
The text of this article originally appeared in Aerospace Testing International.
First test success for largest Mars mission parachute
In March 2018, Swedish Space Corporation, Esrange: Vorticity led the test team to deploy the largest parachute ever to fly on a Mars mission for the upcoming ExoMars RSP mission that will deliver a rover and a surface science platform to the Red Planet.
ExoMars industrial team

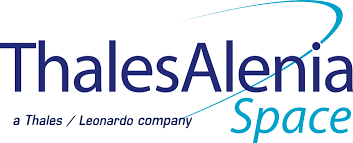

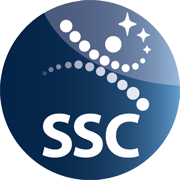
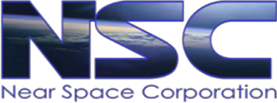